У післявоєнний період (наприкінці 40-х р. XX ст.) активний розвиток машинобудування та металургії, авіаційної та ракетної техніки спричинив пошуки нових матеріалів та досконалих методів і технологій їх обробки.
Конструктори нової техніки прагнули створити більші вироби, які можна виготовляти відразу цілком або з мінімальною кількістю частин. У таких галузях як літакобудування, транспортне машинобудування, ракетобудування таке прагнення зумовлено вимогою створення ідеальних цілісних поверхонь, які могли б полегшити рух та знизити опір середовища при переміщенні автомобілів, літаків або ракет на великих швидкостях.
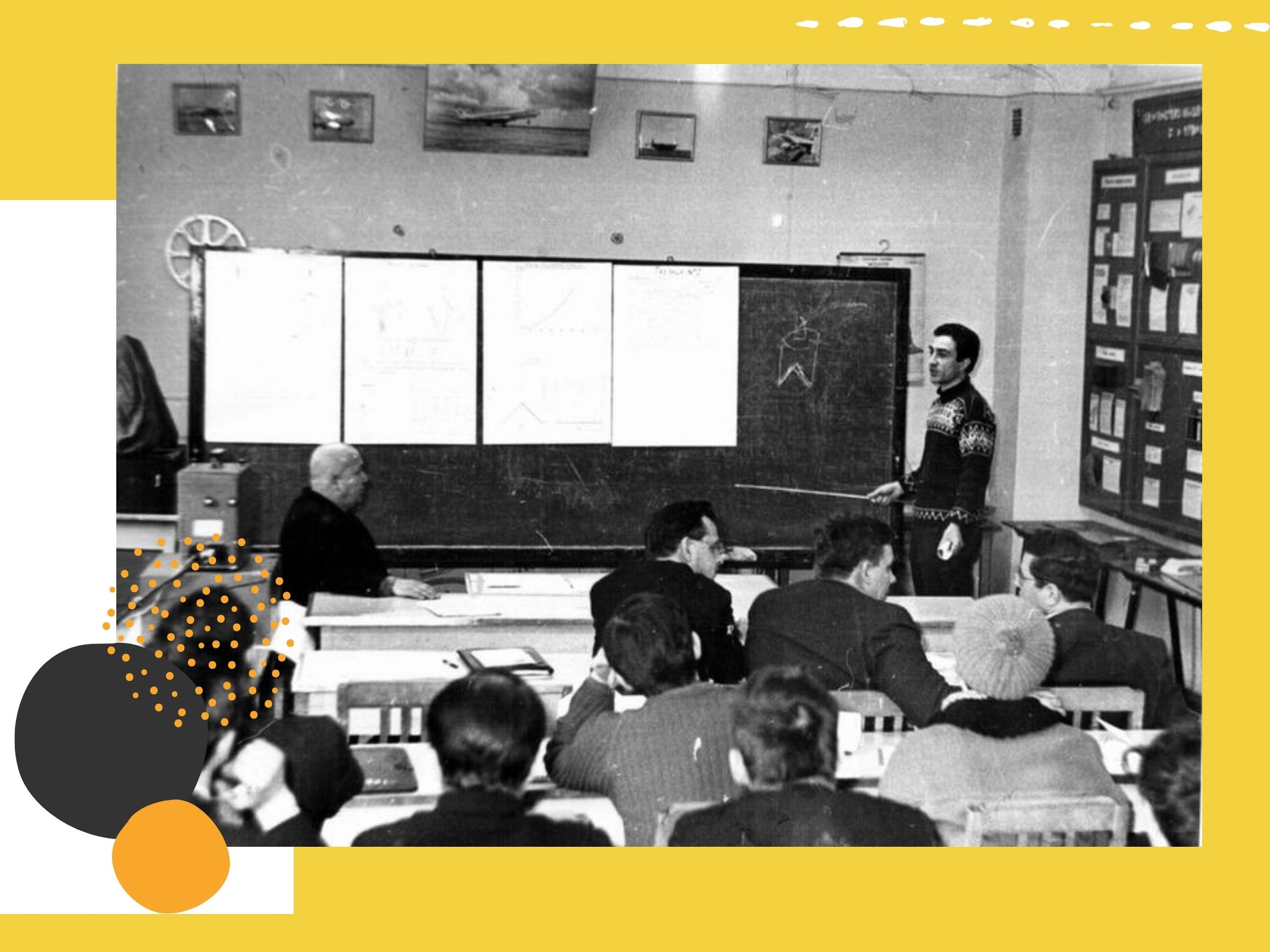
Застосування в окремих галузях промисловості металів та сплавів з дуже високою межею міцності для виготовлення великогабаритних деталей, попит промисловості підштовхнули до пошуку нових технологічних методів формозміни заготовок. Одним із таких став, запропонований в Харківському авіаційному інституті в середині минулого сторіччя, спосіб імпульсної обробки металів тиском за допомогою потоку енергії високої щільності, яка утворюється при швидкісному горінні пороху або бризантних речовин.
У виконанні наукових досліджень, які стосуються обробки металів тиском за допомогою імпульсних вибухових технологій, брав участь колектив викладачів та співробітників науково-дослідницького сектору. Одним з них був Вадим Григорович Кононенко. Він очолив комплекс науково-дослідницьких та дослідних робіт.
Аналіз ідей та пропозицій дозволив виокремити низку технологічних задумок та кінематичних схем пристроїв для втілення в реальні процеси та конструкції. Оскільки серед запропонованих процесів значна кількість була відома, тепер їх можна було реалізовувати за нових незвичних обставин та інноваційних умов. Ці відомі процеси відносились до галузі обробки матеріалів тиском, однак тепер до цього ще додались слова «високошвидкісна, динамічна, ударна», а глибоких, суттєвих знань щодо механічних властивостей металів, що піддаються обробці при новому діапазоні швидкостей (вище освоєної величини у 7 м/с) не існувало. Тому дослідникам нових методів та засобів обробки матеріалів потрібно було вивчити їх властивості та особливості при високошвидкісному навантаженні в різноманітних температурно-швидкісних умовах. Отримання цих додаткових знань було вкрай необхідно і для спеціалістів-розробників, і для творців нових високоміцних матеріалів, і для конструкторів, і для будівників промислових установок та обладнання.
Перш за все, потрібно було приділити увагу дослідженню енергетичних джерел. Якщо раніше при штамповці вибухом використовували, як правило, енергію бризантних вибухових речовин, то при вивченні та експериментах для розгону бійчика з інструментом доцільніше та безпечніше було застосовувати такі хімічні матеріали, які реагують повільніше – порох та метальні (балістичні). На їх основі енергетичний вузол експериментального стенду або установки вийшов достатньо простим, коли потрібно було отримати кількість енергії, що виміряється кількома кілоджоулями (кДж). Для отримання такої кількості енергії було достатнього порохового заряду, який помістився би, наприклад, в об’ємі гільзи гвинтівкового або мисливського стрілецького патрону.
Використання такого енерговузла спричинило створення низки малогабаритних, як правило, переносних пристроїв для виконання технологічних операцій, які не потребують великої енергоозброєності, але достатньо потужних, легких, простих в обслуговуванні та зручних для експлуатації у виробничих та польових умовах.
Одним із перших технологічних процесів, які отримали реалізацію в робочих зразках обладнання, були високошвидкісне пробивання отворів діаметром до 25 мм. в стінках рейок та стальних балках товщиною до 45 мм. для розміщення з’єднувальних та монтажних елементів. Особливістю таких пристроїв була їх автономність, тобто незалежність від зовнішніх джерел енергії, яка характерна для усіх установок з пороховим енерговузлом. Сюди слід віднести також імпульсне клепання нахолодно стальних заклепок великого (до 22 мм.) діаметру, що було важливо під час польових монтажних робіт в машинобудуванні, авіа- та кораблебудуванні, автомобільному виробництві, будівництві котлів та мостів.
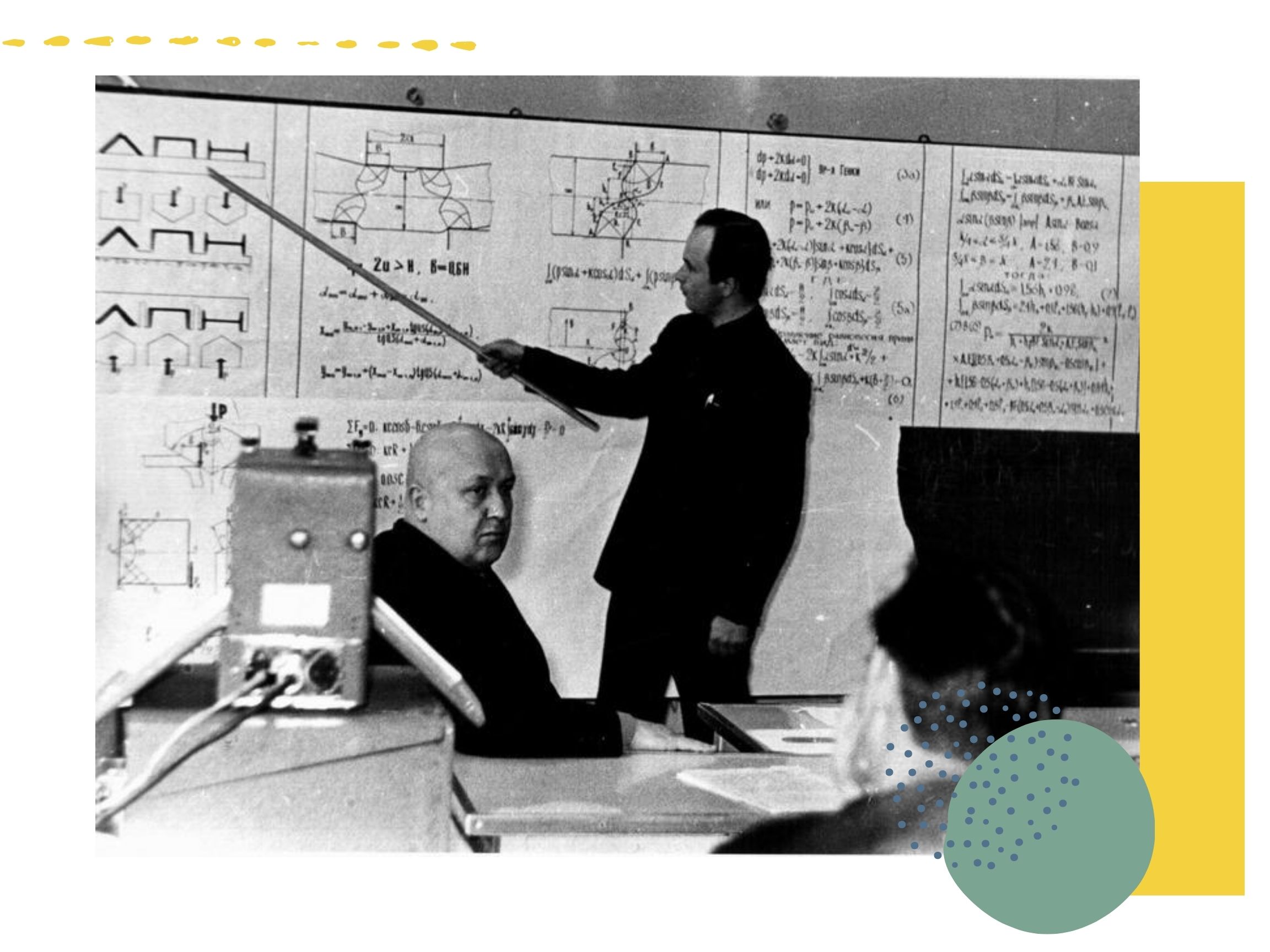
Користуватися попитом почали переносні автономні прилади для імпульсного розвальцьовування кінців труб в трубних дошках котлів та теплообмінників. Порівняно з ручним розвальцьовуванням значно збільшилась продуктивність, підвищилась якість з’єднань, оскільки вони стали більш міцними.
У турбінобудуванні за допомогою спеціалізованих імпульсних пристроїв виконують демонтаж лопаток проточної частини роторів під час ремонтно-відновлювальних робіт, розкарбовують шипи лопаток на бандажах перших ступенів парових турбін під час первинних складально-монтажних операцій та в процесі ремонтних робіт.
Автономність пристроїв для одноударного імпульсного маркування (клеймування) виробів також успішно використовується в металургії та машинобудуванні. За такого способу клеймо утворюється швидко з високою чіткістю знаків та стійкістю до атмосферних та механічних впливів. Клейматор особливо зручний при нанесенні інформації на великі розпечені заготовки.
Підсумки наукових розробок та результати їх практичної реалізації, виконані колективом співробітників та особисто В. Г. Кононенко знайшли своє відображення у численних публікаціях та монографіях.
Конструктори нової техніки прагнули створити більші вироби, які можна виготовляти відразу цілком або з мінімальною кількістю частин. У таких галузях як літакобудування, транспортне машинобудування, ракетобудування таке прагнення зумовлено вимогою створення ідеальних цілісних поверхонь, які могли б полегшити рух та знизити опір середовища при переміщенні автомобілів, літаків або ракет на великих швидкостях.
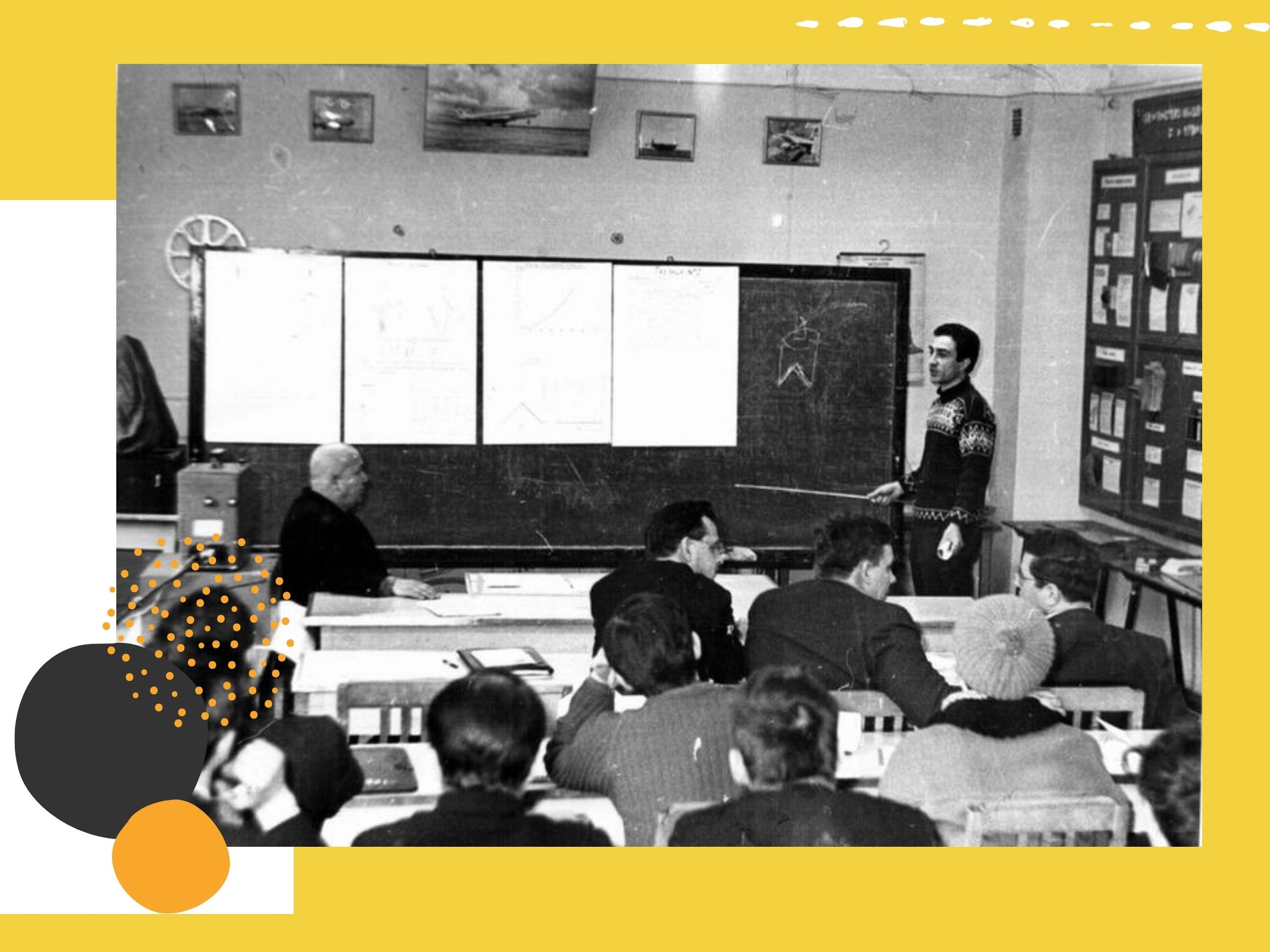
Застосування в окремих галузях промисловості металів та сплавів з дуже високою межею міцності для виготовлення великогабаритних деталей, попит промисловості підштовхнули до пошуку нових технологічних методів формозміни заготовок. Одним із таких став, запропонований в Харківському авіаційному інституті в середині минулого сторіччя, спосіб імпульсної обробки металів тиском за допомогою потоку енергії високої щільності, яка утворюється при швидкісному горінні пороху або бризантних речовин.
У виконанні наукових досліджень, які стосуються обробки металів тиском за допомогою імпульсних вибухових технологій, брав участь колектив викладачів та співробітників науково-дослідницького сектору. Одним з них був Вадим Григорович Кононенко. Він очолив комплекс науково-дослідницьких та дослідних робіт.
Аналіз ідей та пропозицій дозволив виокремити низку технологічних задумок та кінематичних схем пристроїв для втілення в реальні процеси та конструкції. Оскільки серед запропонованих процесів значна кількість була відома, тепер їх можна було реалізовувати за нових незвичних обставин та інноваційних умов. Ці відомі процеси відносились до галузі обробки матеріалів тиском, однак тепер до цього ще додались слова «високошвидкісна, динамічна, ударна», а глибоких, суттєвих знань щодо механічних властивостей металів, що піддаються обробці при новому діапазоні швидкостей (вище освоєної величини у 7 м/с) не існувало. Тому дослідникам нових методів та засобів обробки матеріалів потрібно було вивчити їх властивості та особливості при високошвидкісному навантаженні в різноманітних температурно-швидкісних умовах. Отримання цих додаткових знань було вкрай необхідно і для спеціалістів-розробників, і для творців нових високоміцних матеріалів, і для конструкторів, і для будівників промислових установок та обладнання.
Перш за все, потрібно було приділити увагу дослідженню енергетичних джерел. Якщо раніше при штамповці вибухом використовували, як правило, енергію бризантних вибухових речовин, то при вивченні та експериментах для розгону бійчика з інструментом доцільніше та безпечніше було застосовувати такі хімічні матеріали, які реагують повільніше – порох та метальні (балістичні). На їх основі енергетичний вузол експериментального стенду або установки вийшов достатньо простим, коли потрібно було отримати кількість енергії, що виміряється кількома кілоджоулями (кДж). Для отримання такої кількості енергії було достатнього порохового заряду, який помістився би, наприклад, в об’ємі гільзи гвинтівкового або мисливського стрілецького патрону.
Використання такого енерговузла спричинило створення низки малогабаритних, як правило, переносних пристроїв для виконання технологічних операцій, які не потребують великої енергоозброєності, але достатньо потужних, легких, простих в обслуговуванні та зручних для експлуатації у виробничих та польових умовах.
Одним із перших технологічних процесів, які отримали реалізацію в робочих зразках обладнання, були високошвидкісне пробивання отворів діаметром до 25 мм. в стінках рейок та стальних балках товщиною до 45 мм. для розміщення з’єднувальних та монтажних елементів. Особливістю таких пристроїв була їх автономність, тобто незалежність від зовнішніх джерел енергії, яка характерна для усіх установок з пороховим енерговузлом. Сюди слід віднести також імпульсне клепання нахолодно стальних заклепок великого (до 22 мм.) діаметру, що було важливо під час польових монтажних робіт в машинобудуванні, авіа- та кораблебудуванні, автомобільному виробництві, будівництві котлів та мостів.
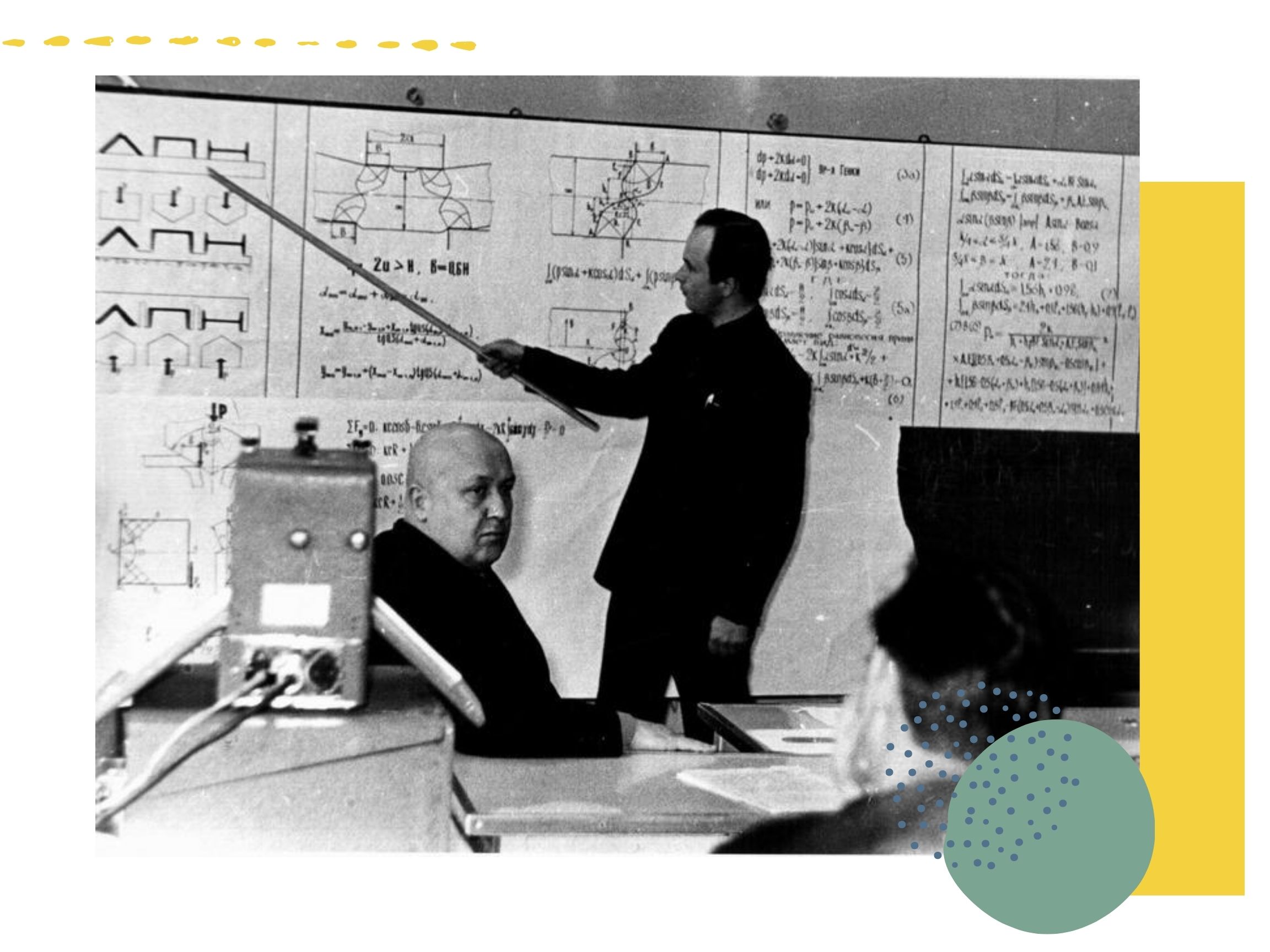
Користуватися попитом почали переносні автономні прилади для імпульсного розвальцьовування кінців труб в трубних дошках котлів та теплообмінників. Порівняно з ручним розвальцьовуванням значно збільшилась продуктивність, підвищилась якість з’єднань, оскільки вони стали більш міцними.
У турбінобудуванні за допомогою спеціалізованих імпульсних пристроїв виконують демонтаж лопаток проточної частини роторів під час ремонтно-відновлювальних робіт, розкарбовують шипи лопаток на бандажах перших ступенів парових турбін під час первинних складально-монтажних операцій та в процесі ремонтних робіт.
Автономність пристроїв для одноударного імпульсного маркування (клеймування) виробів також успішно використовується в металургії та машинобудуванні. За такого способу клеймо утворюється швидко з високою чіткістю знаків та стійкістю до атмосферних та механічних впливів. Клейматор особливо зручний при нанесенні інформації на великі розпечені заготовки.
Підсумки наукових розробок та результати їх практичної реалізації, виконані колективом співробітників та особисто В. Г. Кононенко знайшли своє відображення у численних публікаціях та монографіях.
Назад